59 ProForm Exercise Bike Manuals and User Guides (62 Models) were found in All-Guides Database
- Whirlwind 185 TAG STRINGER AND KNOTTER Model: whirlwind 185 SOLD Serial No.: machine NO K-1248 Manufacturer: GRAEBER: TAG STRINGER Whirlwind 185: Previous 5: Back to TOP OF PAGE: www.BarbersUsedMailingEquipment.com Email: BuySell@BarbersUsedMailingEquipment.com.
- Download this manual and access the complete library. Model 190 & 195. R-790 Whirlwind. R-975 Whirlwind 9 - J6.
Motorized blinds and shades are a stylish, rewarding investment in comfort, convenience, and peace of mind. Motorized Blinds and Shades Match your needs with a specific Graber window treatment solution Graber Product Advisor Preview window treatments on your own window—easily upload a photo! Or choose from our sample room scenes. View and Download Pro-Form Whirlwind air user manual online. Bike exerciser. Whirlwind air Exercise Bike pdf manual download. Also for: 831.21922.0.
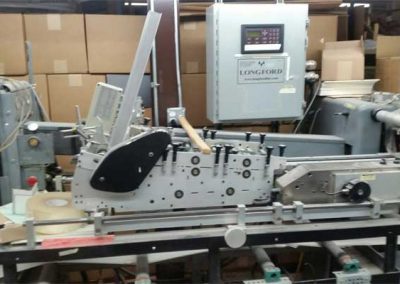
ProForm Exercise Bike: List of Devices
# | Model | Type of Document |
---|---|---|
21 | ProForm 975S | |
22 | ProForm 990 S | ProForm Exercise Bike 990 S Operation & user’s manual (16 pages) |
23 | ProForm PFEL05807 | ProForm Exercise Bike PFEL05807 Operation & user’s manual (28 pages) |
24 | ProForm PFEX17910 | ProForm Exercise Bike PFEX17910 Operation & user’s manual (16 pages) |
25 | ProForm PFEX72411.1 | ProForm Exercise Bike PFEX72411.1 Operation & user’s manual (24 pages) |
26 | ProForm PFEXF495.0 | ProForm Exercise Bike PFEXF495.0 Operation & user’s manual (20 pages) |
27 | ProForm SR 20 | ProForm Exercise Bike SR 20 Operation & user’s manual (12 pages) |
28 | ProForm SR 30 | |
29 | ProForm WHIRLWIND AIR | ProForm Exercise Bike WHIRLWIND AIR Operation & user’s manual (24 pages) |
30 | ProForm XP 100 U | |
31 | ProForm XP 185 U | ProForm Exercise Bike XP 185 U Operation & user’s manual (24 pages) |
32 | ProForm XP 210 U | ProForm Exercise Bike XP 210 U Operation & user’s manual (24 pages) |
33 | ProForm XP WhirlWind 280 |
ProForm Exercise Bike: Popular and Often Search Manuals
ProForm Exercise Bike XP400 R
ProForm Exercise Bike Operation & user’s manual (24 pages)ProForm Exercise Bike 300 ZLX
ProForm Exercise Bike Operation & user’s manual (24 pages)ProForm Exercise Bike 485E
ProForm Exercise Bike Operation & user’s manual (16 pages)ProForm Exercise Bike PFEX72411.1
ProForm Exercise Bike Operation & user’s manual (24 pages)ProForm Exercise Bike 831.21952.3
ProForm Exercise Bike Operation & user’s manual (24 pages)ProForm Exercise Bike 5.5 Crosstrainer Treadmill
ProForm Exercise Bike Operation & user’s manual (24 pages)ProForm Exercise Bike WHIRLWIND AIR
ProForm Exercise Bike Operation & user’s manual (24 pages)ProForm Exercise Bike XP WhirlWind 280
ProForm Exercise Bike Operation & user’s manual (20 pages)ProForm Exercise Bike 990 S
ProForm Exercise Bike Operation & user’s manual (16 pages)ProForm Exercise Bike 831.288300
ProForm Exercise Bike Operation & user’s manual (16 pages)ProForm Exercise Bike SR 30
ProForm Exercise Bike Operation & user’s manual (16 pages)ProForm Exercise Bike XP440 R
ProForm Exercise Bike Operation & user’s manual (24 pages)ProForm Exercise Bike XP WhirlWind 280
ProForm Exercise Bike Operation & user’s manual (20 pages)ProForm Exercise Bike PFEX01416.1
ProForm Exercise Bike Operation & user’s manual (40 pages)ProForm Exercise Bike PFEXF495.0
ProForm Exercise Bike Operation & user’s manual (20 pages)ProForm Exercise Bike Saturn2 PFIVEX73513.0
ProForm Exercise Bike Operation & user’s manual (16 pages)ProForm Exercise Bike SR 20
ProForm Exercise Bike Operation & user’s manual (12 pages)ProForm Exercise Bike 110 R
ProForm Exercise Bike Operation & user’s manual (24 pages)ProForm Exercise Bike 831.28822
ProForm Exercise Bike Operation & user’s manual (12 pages)ProForm Exercise Bike XP WhirlWind 280
ProForm Exercise Bike Operation & user’s manual (20 pages)ProForm Exercise Bike 831.21942.1
ProForm Exercise Bike Operation & user’s manual (24 pages)ProForm Exercise Bike XP WhirlWind 280
ProForm Exercise Bike Operation & user’s manual (20 pages)ProForm Exercise Bike 490 Spx Bike
ProForm Exercise Bike Operation & user’s manual (24 pages)ProForm Exercise Bike 225 CSX
ProForm Exercise Bike Operation & user’s manual (28 pages)ProForm Exercise Bike 831.21752.0
ProForm Exercise Bike Operation & user’s manual (24 pages)ProForm Exercise Bike 210 Csx Bike
ProForm Exercise Bike Operation & user’s manual (28 pages)ProForm Exercise Bike 770s PFEX72060
ProForm Exercise Bike Operation & user’s manual (8 pages)ProForm Exercise Bike XP 185 U
ProForm Exercise Bike Operation & user’s manual (24 pages)ProForm Exercise Bike XP 210 U
ProForm Exercise Bike Operation & user’s manual (24 pages)ProForm Exercise Bike Le Tour De France PFEVEX71316
ProForm Exercise Bike Operation & user’s manual (32 pages)ProForm Exercise Bike 920 S EKG 831.280170
ProForm Exercise Bike Operation & user’s manual (16 pages)ProForm Exercise Bike 831.21942.2
ProForm Exercise Bike Operation & user’s manual (24 pages)ProForm Exercise Bike 275 ZLX
ProForm Exercise Bike Operation & user’s manual (16 pages)ProForm Exercise Bike PFEL05807
ProForm Exercise Bike Operation & user’s manual (28 pages)ProForm Exercise Bike XP 100 U
ProForm Exercise Bike Operation & user’s manual (20 pages)ProForm Exercise Bike PFEX17910
ProForm Exercise Bike Operation & user’s manual (16 pages)ProForm Exercise Bike 975S
ProForm Exercise Bike Operation & user’s manual (16 pages)
VH-19B U.S. Air Force Serial No. 53-4436
.
Background
The Sikorsky S-55 helicopter was a utility helicopter developed with company funds and without government sponsorship. Sikorsky designed and fabricated a mockup of an entirely new model with many novel features in less than one year. Its most significant novel features included unique placement of its piston engine and the incorporation of offset hinges in its main rotor head. Engine placement below and forward of the cockpit resulted in a large cabin directly below the main rotor and the rotor’s offset hinges provided large control moments to enable a wide center-of-gravity range. The result was achievement of nearly unrestricted placement of passengers or cargo in a relatively spacious cabin. Both of these novel features were major departures from Sikorsky’s earlier configuration as embodied in the R-4,R-5 and R-6 models and were responsible for the development of a highly successful design well suited to larger utility helicopter models. This configuration, as embodied first in the S-55, led to Sikorsky capturing a major share of the worldwide utility market and it further led to foreign competitors copying this configuration. Of the many helicopter designers who helped develop this new configuration, Edward F. Katzenberger provided the creative spark that made it all come together successfully.
The first customer was the U.S. Air Force who ordered five YH-19 helicopters for service evaluation. First flight was on November 10, 1949 less than a year from the program start date. The S-55 helicopter was a giant step forward for Sikorsky helicopter designs and with its 10 passenger capacity and the 2,000 pound external lift capacity was a true transport helicopter. The Air Force deployed a YH-19 helicopter to Korea in March 1951 for evaluation and the day after arrival it assisted in evacuating paratroops.
In addition to its new engine placement and its main rotor offset hinges, theS-55 also featured all metal main and tail rotor blades which had been introduced on late model S-51 helicopters. Hydraulic main rotor servos, also introduced on late model S-51 helicopters, provided “Power Steering” for the pilots and eliminated main rotor control loads from reaching the cockpit control sticks..
YH-19 First Flight November 10, 1949
The S-55 was designed for easy maintenance. The clam shell doors on the nose provided full access to the engine compartment. such that an engine change required only 2 hours. The main rotor head/main gearbox assembly Quick Change Unit (QCU) required only 3 hours to replace. It was possible to change every major component including engine, clutch, main transmission, main rotor head, flight control system intermediate transmission, tail gear box, and tail rotor head in 12-15 man-hours or in as little as 5 hours elapsed time.
The S-55 was air transportable in C-82, C-119, and C-124 aircraft.
Sikorsky S-55 side view cutaway
Customer | Model No. | Old Model No. Prior to 1962 | Nickname | Mission |
US Air Force | YH-19 | Service Evaluation | ||
US Air Force | UH-19A | H-19A | Utility 600 hp P&W Eng. | |
US Air Force | HH-19A | SH-19A | Search and Rescue (SAR) | |
US Air Force | UH-19B | H-19B | Utility 700 hp Wright Eng. | |
US Air Force | HH-19B | SH-19B | Utility 700 hp Wright Eng. | |
US Navy | HO4S-1 | Utility 600 hp P&W Eng. | ||
US Navy | UH-19F | HO4S-3 | Utility 700 hp Wright Eng. | |
US Navy | SH-19F | HO4S-3 | ASW 700 hp Wright Eng. | |
US Coast Guard | HH-19G | HO4S-3G | ASW 700 hp Wright Eng. | |
US Army | UH-19C | H-19C | Chickasaw | Utility 600 hp P&W Eng. |
US Army | UH-19D | H-19D | Chickasaw | Utility 700 hp Wright Eng |
U. S. Marine Corps. | HRS-1 | Utility 600 hp P&W Eng. | ||
U. S. Marine Corps | HRS-2 | Utility 600 hp P&W Eng. | ||
U. S. Marine Corps | CH-19E | HRS-3 | Utility 700 hp Wright Eng. | |
Commercial | S-55 | Passengers/Cargo 600 hp P&W Eng. | ||
Commercial | S-55B | Converted Military models with 700 hp Wright Eng. | ||
Commercial | S-55C | FAA Improved Model. 600 hp P&W Eng. | ||
Commercial | S-55D | Export Model. 700 hp Wright Eng | ||
Westland Whirlwind | HRS-2 | HAR.21 | HRS-2 for Royal Navy | |
Westland Whirlwind | HO4S-3 | HAS.22 | HO4S-3for Royal Navy |
Military Service
All U.S. Military services ordered the S-55. The Air Force identified it as the H-19, the Navy and Coast Guard as an HO4S, the Marine Corps as an HRS, and the Army as a CH-19. This was before 1962, when all U.S. military services adopted a uniform model identification system.
Military Helicopter Developments
U.S. Air Force
The first YH-19 arrived in Korea in March, 1951 for service testing with a second arriving in September, 1951.
U.S. Air Force YH-19 helicopter in Korea 1951
Based on successful operational testing, the U.S. Air Force ordered 50 production H-19A helicopters. On July 15 1952 two H-19A helicopters named Hop-A-Long and Whirl-O-Way, stripped of all unnecessary equipment and with three 100 gallon auxiliary fuel tanks in the cabin, self-deployed from Westover AFB, Massachusetts to Wiesbaden AFB, Germany. The first transatlantic crossing by helicopter followed a great circle route via Presque Isle, Maine - Goose Bay, Labrador - Narsarsuaq, Greenland - Keflavik, Iceland - Prestwick, Scotland. After welcoming ceremonies in Scotland, the 2 helicopters continued on to Schiphol, Holland and arrived at Wiesbaden AFB, Germany on August 4, 1952, a 4,220 mile trip. The longest leg of this trip was the 850 mile over water leg from Keflavik, Iceland to Prestwick, Scotland.
H-19A Air Force Serial No. 51-389 landing at Prestwick, Scotland after first Transatlantic crossing
U.S. Air Force H-19 helicopters performed many rescues in Korea including night rescues and rescues behind enemy lines. Others duties included transferring wounded from the field to Mobile Army Surgical Hospital (MASH) units and from MASH units to larger hospitals, and inserting/retrieving Allied agents behind enemy lines. The 3rd Air Rescue Squadron evacuated over 7,000 wounded during the Korean War utilizing both H-5 and H-19 helicopters. They also rescued 170 pilots from behind enemy lines and from the Yellow Sea.
U.S. Air Force SH-19B rescues a pilot from the sea. Korea - 1953
U.S. Navy
HO4S-1 helicopters started arriving in 1952 to replace the HO3S-1 helicopters. The first HO4S-1 helicopter was delivered to Helicopter Utility Squadron HU-2 at NAS Lakehurst, N.J. Later Helicopter Utility Squadrons HU-1 San Diego California was equipped with some HO4S-1 models which saw limited service in Korea.
HU-1 HO4S and HO3S on LST 735 Wonsan Harbor Korea 1953
U.S. Marine Corps
HMR-161 arrived in Korea on September 2, 1951 with 15 HRS-1 helicopters. The new helicopter squadron wasted no time in demonstrating their capabilities. On September 13, 1951 HMR-161, during Operation Windmill I, transported 18,848 pounds of gear and 74 Marines into a ridgeline position in the Punchbowl area. A week later HMR-161 shuttled 224 Recon Company Marines and 17,772 pounds of supplies to a remote hilltop in the same area.
Their performance continued to improve and in Operation Haylift II in February 23-27, 1953, HMR-161 lifted 1.6 million pounds of cargo to resupply two regiments. Although HMR-161 helicopters were operating in hot landing zones they did not lose any helicopters to enemy fire.
HRS-1 helicopters were also used to relocate Rocket Launcher Batteries. Because rockets create much visible dust when fired they make an easy target for enemy artillery. To reduce their exposure, men and launchers were moved twice a day. HRS-1 helicopters carried four rocket launchers and extra rockets as external cargo with the crew in the cabin.
The HRS-1 helicopter proved to be durable and reliable. One reportedly flew home after losing 18 inches of main rotor blade to a tree. HMR-161 reported 90% aircraft availability.
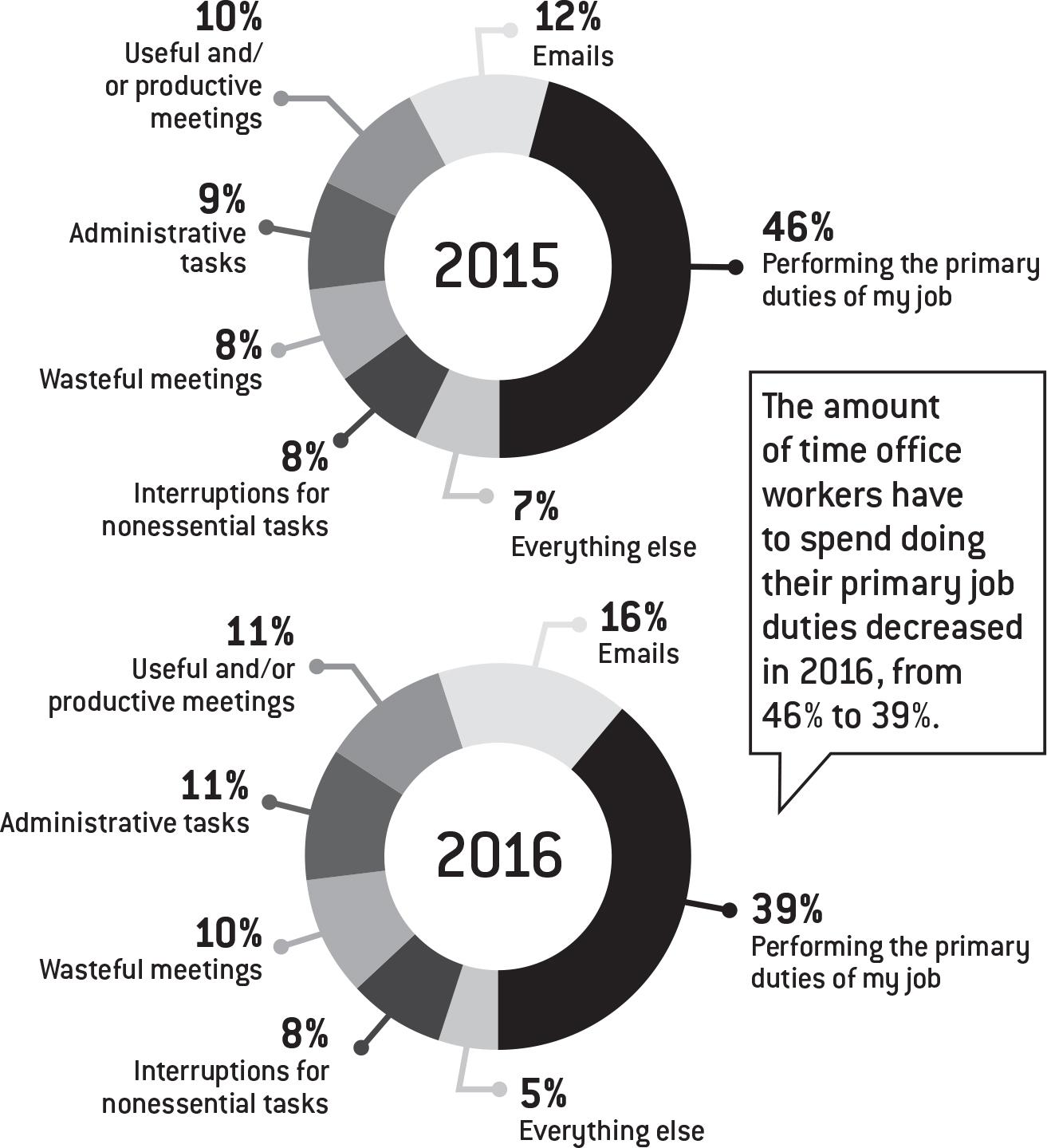
USMC HRS-1 picks up stranded Marines - Korea 1951
U.S. Army
The U.S. Army was late in arriving in Korea after successfully overcoming a U.S. Air Force objection to the Army acquiring “heavy” helicopters. The first unit, the 6th Transportation Company (Helicopter) arrived in March 1953. They immediately went to work resupplying forward elements of the 3rd Division that were cut off by floods on March 20, 1953. Ten H-19 C helicopters in 30 round trips provided 33,925 pounds of food, ammunition, and charcoal to a landing spot 300 yards from a main line of resistance. In June 1953 the Army and Marines joined forces in the largest helicopter operation of the war using 45 helicopters to move 800 Republic of Korea (ROK) troops.
H-19C U.S. Army Serial No. 51-14284 loading troops in Korea
Anti Submarine Warfare (ASW)
The U. S. Navy purchased 10 HO4S-1 helicopters. Some of these were assigned to the newly formed HS-1 at NAS Key West, Florida. Their mission was to develop helicopter submarine hunter/killers. The HO4S-1 proved to be underpowered for the mission. The Navy then tried the Piasecki HUP-1 tandem rotor helicopter which was also proved to be underpowered for the mission. When the HO4S-3 helicopter equipped with the R-1300 700 hp engine became available it proved to be adequate for the mission. The Navy then had its first operational daylight VFR ASW helicopter.
S-55 Commercial Helicopters
The commercial model of the S-55 helicopter received Civil Aviation Agency (CAA) certification on March 25, 1952. The first customer was New York Airways which established service between the three New York area airports on July 9, 1953 becoming the first scheduled helicopter airline to carry passengers in the United States. Service was later expanded to include a Heliport at W.30th Street and the West Side Highway and service to Teterboro Airport, N.J., White Plains, N.Y., and Stamford Connecticut.

New York Airways S-55 with soft floats for its overwater routes
S-55 sales continued with deliveries to Los Angeles Helicopter Airline which was upgrading from their S-51 helicopters. Sales to Canada were made commercially through the Canadian Subsidiary of Pratt & Whitney. Foreign sales to Belgium (SABENA), Japan, India and, Argentina followed. Petroleum Helicopters purchased their first S-55 in 1954 to support oil operations in the Gulf of Mexico.
On October 3, 1956 the S-55C with an inclined tail cone to prevent main rotor blades from contacting the tail cone during hard landings was certified by the CAA. Sikorsky continued to use the 600 hp Pratt & Whitney engine on the S-55C model.
With its 2,000 lbs. of external cargo capability, the S-55 was popular for construction projects in inaccessible areas. In Canada, the S-55 was used by Okanagan Helicopters Services to build a hydroelectric and bauxite smelting projects for Aluminum Company of Canada some, 500 miles from Vancouver in the wilds of British Columbia. A 50 mile power transmission line requiring 350 towers at elevations up to 5,300 feet was erected by the S-55 helicopters. Components for the transmission lines, supplies, men, and a complete camp to support 125 men were lifted into a mountain pass.
S-55C delivering cargo in Canada
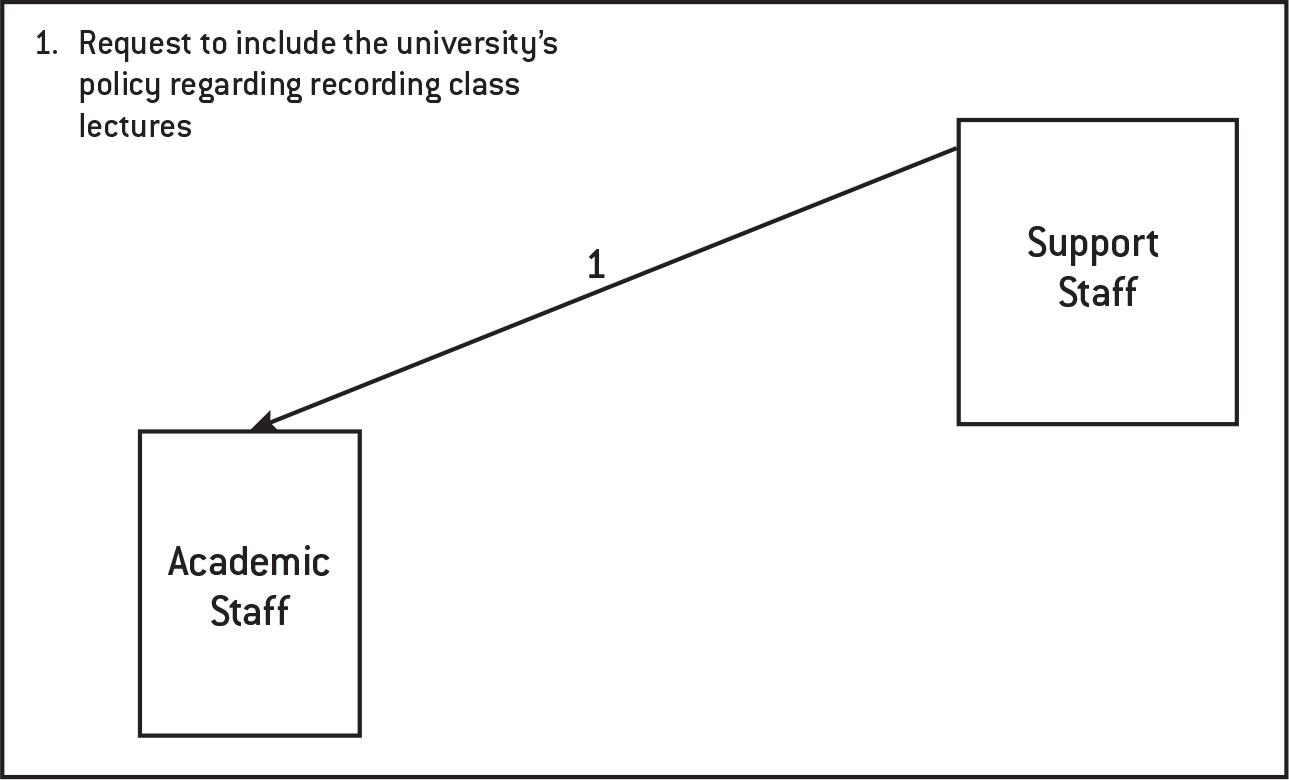
.Both commercial S-55C and Royal Canadian Air Force H-19 helicopters were utilized to build the Distant Early Warning (DEW) line, an early warning radar system designed to warn of a USSR bomber attack on the United States and Canada. Building supplies and construction personnel were hauled to building sites in spite of an inhospitable climate.
S-55C constructing the DEW line in Northern Canada
.S-55 Development Timeline
- November 10, 1949First Flight of the S-55
- April 16, 1950. Delivery of first YH-19 to the U.S. Air Force
- August 31, 1950. Delivery of the first HO4S-1 helicopter to the U. S. Navy
- March, 1951. First YH-19 deployed to Korea
- April 27, 1951. First HRS-1 helicopter delivered to the U. S. Marine Corps.
- May 2, 1951. First S-55 helicopter delivered to Westland.
- September 2, 1951 Marine squadron HMR-161 arrived in Korea with 15 HRS-1 helicopters.
- November 15, 1951. First HO4S-1G delivered to the U.S. Coast Guard.
- December 22, 1951. First H-19 helicopter delivered to U. S. Air Force.
- January 16, 1952. License agreement signed with SNCASE (France)
- March 25, 1952 S-55 CAA type certification.
- March 31, 1952. First commercial S-55 delivered to New York Airways.
- June 8, 1952. First S-55 delivered to Los Angeles Airways.
- July 1952. First transatlantic self-deployment by 2 U.S. Air Force H-19A helicopters to Europe.
- March 20, 1953 U.S. Army 6th Transportation Company flew the first mission with H-19A helicopters
- October 3, 1956. S-55C (Inclined tail cone) CAA certification.
- February 26, 1969. U.S. Navy Squadron HC-5 retires last CH-19E in U. S. Military service.
.
.
Configuration Features
S-55 Military Model Main Differences Table
ITEM | HRS/HO4S-1 | HRS/HO4S-2 | HRS/HO4S-3 | H -19A | H-19B | H-19C | H-19D |
Engine | R-1340-57 | R-1340-57 | R-1300-3 | R-1340-57 | R-1300-3 | R-1340-57 | R-1300-3 |
Carburetor | Float Type – Manual Lean | Float Type – Manual Lean | Pressure Injection – Auto Lean | Float Type – Manual Lean | Pressure Injection – Auto Lean | Float Type – Manual Lean | Pressure Injection – Auto Lean |
Clutch | Automatic-Centrifugal | Automatic-Centrifugal | Hydro-Mechanical | Automatic-Centrifugal | Hydro-Mechanical | Automatic-Centrifugal | Hydro-Mechanical |
Tail Cone | Straight | Inclined down 3 degrees | Inclined down 3 degrees | Straight | Inclined down 3 degrees | Straight | Inclined down 3 degrees |
Tail Rotor Diameter | 8’8” | 8’9” | 8’9” | 8’8” | 8’9” | 8’8” | 8’9” |
Stabilizer | Inverted V | Inverted V | Horizontal | Inverted V | Horizontal | Inverted V | Horizontal |
Rescue Hoist | 400 lbs | 400 lbs | Some 400 #, later 600 lbs. | SH models 400 lbs. | SH models 600 lbs. | None | None |
Aux Servo – Lateral Only | Yes | Yes | Yes |
.
Fuselage
The Sikorsky S-55 fuselage was an aluminum framed cabin with aluminum and magnesium skins. Plexiglas windows surrounded the pilot and copilot sitting above and behind the engine with the engine driveshaft between the seats. Cabin seating was provided for 10 passengers or 6 litters and a medic. Civilian models provided cabin seating for 7 passengers. A hatch was provided in the cabin floor to allow the crew to observe cargo hook external loads and provide direction to the pilot.
The S-55 helicopters were modified to several different configurations during their years of service. In addition to the civilian S-55 and S-55C models, the S-55 was operated by the U.S Navy as the HO4S /USMC as HRS, the USAF as H-19, SH-19, and the USCG as the HO4S-2/3G. Surplus military models for all services could be modified and FAA Certified as the S-55 and S-55B.
Main Rotor Assembly
A 3 bladed fully articulated main rotor head with an offset flapping hinge (9 inches for the rotor centerline) which increased the allowable center of gravity limits and improved handling qualities was installed on the S-55 helicopter. The rotor diameter was 53 feet.
A hydraulic servo system provided power assist to the flight controls and eliminated feedback of main rotor vibrations to the cockpit. Two fingers were all that was required to move the cyclic pitch stick in flight.
.
S-55 Main Rotor Assembly.
Tail Rotor Assembly
A 2 bladed 8’ 8” diameter tail rotor with all metal blades was installed on the S-55 helicopter. A 2 bladed 8’ 9” diameter tail rotor with all metal blades was installed on later model S-55 helicopters with the inclined tail cone which prevented the main rotor blades from contacting the tail cone during a hard landing.
Main Gear Box
The main gear box contained a spiral bevel gearing stage followed by a two stage planetary reduction gear system which reduced engine rpm at a 11.3155 to 1 ratio for driving the main rotor. Take-off shafting from the main gear box housing extended aft to the intermediate gear box and then back to the tail rotor gear box and tail rotor. Accessories driven by the main gear box were the generator, generator blower, flight control servo hydraulic pump, rotor tachometer generator, and main gear box oil pump. A freewheeling unit in the input section of the main gear box disconnected the engine from the main gear box allowing autorotation in the event of engine failure.
S-55 Main Gear Box and Hydraulic Servos
Engine
Sikorsky’s chief of advanced design and later chief engineer, Edward F. Katzenberger, created the first major innovation to increase the allowable center of gravity travel in the S-55 design. His idea was to relocate the reciprocating piston engine from under the rotor to a location forward of the cabin and below the cockpit. This was a dramatic configuration change that opened up a spacious cabin compartment directly below the main rotor. As a result, payload could then be carried on or near the aircraft’s center of gravity and essentially in line with the rotor’s rotational axis. This relocation of the engine also made the engine more accessible and maintenance easier by virtue of large clamshell doors that opened to expose the engine at ground level.
A Pratt and Whitney nine cylinder R-1340-57, 600 hp air cooled radial engine was installed at a 35 degree angle in the nose of the helicopter. Later model military S-55 models used a seven cylinder Wright R-1300-3, 700 hp air cooled radial engine. Since the engines were installed in reverse from a conventional installation, the engine accessories were readily serviceable through large clam shell doors.
Wright R-1300-3 engine installation on U.S. Army H-19D serial No. 52-7602.
Hydro-Mechanical Clutch
The Military model S-55 with the R-1300-3 engines incorporated a hydro mechanical clutch which replaced the centrifugal clutch which automatically connected the engine to the main gear box when a certain RPM was reached. This was a first for Sikorsky helicopters. Functions of the hydro mechanical clutch were:
- Pro vide a direct mechanical coupling between the engine and the transmission system.
- Permit engine to be started and operated at any speed when completely disengaged from the transmission system.
- Provide smooth and rapid acceleration of the rotor blades and transmission during clutch engagement.
The hydro mechanical clutch consisted of a hydraulic oil pump and reservoir to a fluid coupling for clutch engagement. Once the clutch completed a direct mechanical connection with the transmission system, the oil pump was turned off and oil drained from the coupling.
Main Rotor Blades
The main rotor blades were constructed with aluminum spars, aluminum ribs, aluminum pockets with a honeycomb filler. All blades were balanced and tabbed on the main rotor blade whirl stand against a master blade and stenciled with the required adjustment on installation. This eliminated the requirement to manually track blades when installing a replacement blade. Later model main rotor blades featured spars pressurized to 10 psi with nitrogen. Indicators were added to the blades which were checked on preflight to confirm spar integrity. This feature was called BIM for Blade Inspection Method. It was invented by Sikorsky and first employed on the S-58 model main rotor blades and then offered to S-55 customers. All metal spar main rotor blades subsequently built included the BIM feature. The BIM system provided a major improvement to flight safety by giving the pilots and/or ground crew a way to determine the structural integrity of the blade spar just prior to flight. An indicator mounted at the blade root end would change color if the spar developed the smallest crack thereby releasing the internal nitrogen pressure which activated the indicator position and visible color change.
General Arrangement Drawing
S-55 3-view Drawing
Mission Systems
Rescue Hoists
400 pound Capacity Hoist. Early S-55 helicopters and all Commercial S-55 helicopters offered a foldable 400 pound capacity rescue hoist which was mounted above the cabin door. The hoist cable ran through a conduit in the cabin to a reel and hydraulic motor in the baggage compartment at the rear of the cabin. A crank on the cabin overhead moved the hoist arm to the hoist position and folded it flat against the fuselage when not in use.
400 pound capacity rescue hoist
600 pound Capacity Hoist. On later model S-55 Military helicopters, a self-contained hoist mounted over the cabin door was provided. This hoist provided an increase in lifting capacity and more reliable service.
600 pound capacity hoist on USCG HO4S-3G
Rescue Basket
The U.S Coast Guard developed a rescue basket which allowed an injured person to be scooped up from the water and recovered. In a rescue on December 24, 1955 at Yuba City California Air Force and Navy helicopters were assisting but only carried a “Horse Collar” for recoveries. After a Navy helicopter dropped a survivor it was decided to allow the Coast Guard to do the lifts and the other helicopters would spot survivors. A single Coast Guard helicopter flying 2 hour shifts, with one pilot and a hoist operator, and refueling without shutting down recovered 138 people in 15 hours of continuous operation.
U.S. Coast Guard HO4S-3G with rescue basket
Rockets on Rotor (ROR)
A Marine HRS-2 helicopter was outfitted with small (1 pound) rocket motors in the Tip Caps of the main rotor blades which added 35 pounds of thrust to each blade. ROR was fueled by hydrogen peroxide with the propellant tank mounted on the top of the main rotor which fueled the system for. The complete system weighed approximately 67 lbs.
Graeber Whirlwind 185 Manual For Sale
The system was developed in conjunction with Sikorsky Aircraft was first test flown by Sikorsky pilots on March 9, 1954. After 6 months of developmental testing, the Marines demonstrated it to the public at NAS Anacostia, Washington, D.C. on September 16, 1954.
The ROR system allowed:
Graeber Whirlwind 185 Manual Parts
- Improved autorotation performance
The development tests were successful and provided many benefits at a modest increase in weight. However, the system was never adapted for any helicopters.
A 1955 video of the ROR produced as a Contract requirement by Reaction Motors Inc. is available at the following link:
General Characteristics and Performance S-55
PERFORMANCE
Standard Day, Sea Level
Maximum speed (Vne) | 95 kts 161 km/hr |
Range | 405 miles 651 km |
Service ceiling | 11,400 ft 4,511 m |
Rate of Climb | 730 ft/min 3.7 m/s |
.
WEIGHTS
S-55 Commercial | |
Maximum takeoff gross weight | 7,200 lbs 3,271 kg |
Weight empty | 4,785 lbs 2,173 kg |
Maximum fuel load | 185 gal 698 ltr |
Useful Load | 2,415 lbs 1,098 kg |
GENERAL DATA
Crew seating capacity | 2 |
Seating capacity (Military model 10 passengers) | 7 passengers |
.
POWERPLANT RATINGS
Standard Day at Sea Level
Pratt and Whitney R-1340 S1H2 (Take Off) | 600 hp 447.6 kw |
Wright R-1300-3 | 700 hp 522.2 kw |
.
AIRCRAFT DIMENSIONS
Main rotor diameter (blade tip circle) | 53’ 0” 16.10 m |
Tail rotor diameter (blade tip circle) 8’ 9” with Drooped Tail | 8’ 8” 2.64 m |
Fuselage length | 42’2' 12.85m |
Length over-all (including rotors) 62’2.5” Drooped Tail | 62’2' 18.99 m |
Height over-all | 13’ 4” 4.07 m |
Main landing gear tread | 11’ 0' 2.64 m |
.
Production History
Sikorsky Aircraft S-55 production consisted of 1281 helicopters. Westland (England), SNCASE (France), and Mitsubishi (Japan) built an additional 477 helicopters under license:
|
---|
During Military service some S-55 helicopters were converted to the 700 hp engine configuration. S-55 helicopters also changed ownership (Air Force to Marines; Marines to Navy and then back to the Marines) sometimes multiple times making accurate tracking difficult.
Military surplus S-55 helicopters were sold on the open market. Sikorsky sold kits and provided instructions for converting military S-55 helicopters to meet CAA (FAA) Certification requirements. These helicopters, identified in the Sikorsky Aircraft S-55 Type Certificatewere registered as the S-55B model. Other military surplus helicopters were modified and FAA Certified as S-55 and S-55B helicopters under a Type Certificate issued to Orlando Helicopter Airways
Related Models
License Built Helicopters
Westland Aircraft Ltd
On November 15, 1950 Sikorsky signed a License agreement with Westland for the S-55 model. The first Westland built WS-55 first flight was on September 14, 1951. Westland built WS-55 Whirlwind helicopters with many Westland designed features.
|
Westland Whirlwind HCC.12 Queen’s Flight Helicopter with Gnome Turboshaft Engine.
SNCASE
A license agreement was signed on January 16, 1952 by Sikorsky with SNCASE (Société Nationale des Constructions Aéronautiques du Sud-Est) to build S-55 helicopters in France. They in turn subcontracted components to Breguet Aviation for cabins and Fiat in Italy for rotor heads.
A License built version of the U.S Army CH-19D built for the French Army, Navy, and Marines and designated the S-55D. Over 100 S-55 helicopters were produced by SNCASE. The French nicknamed the S-55 the Elephant Joyeux (Happy Elephant).
.
Mitsubishi
Mitsubishi Heavy Industries (MHI) signed a License agreement with Sikorsky on April 1, 1958 to build helicopters for the Japanese Self Defense Forces. Over 40 S-55C helicopters were produced by Mitsubishi.
Aftermarket Modifications
S-55T Helicopters modified under a Supplemental Type Certificate (STC) by Aviation Specialties and produced and marketed by Helitec with a 650 shp, Allied Signal TPE-331-3U-303 Turboshaft engine with updated equipment were registered as the S-55T. The conversion removed 900 lbs. from the empty weight of the helicopter.
Heli-Camper. Orlando Helicopters offered a. RV conversion of the S-55 which slept four, complete with a kitchen, toilet, and an awning.
Orlando Helicopters S-55 Heli-Camper, The Flying Winnebago.
S-55QT. Vertical Aviation of Sanford, Florida obtained an Supplemental Type Certificate (STC) for the S-55QT Whisper Jet in 2001. It featured a 5 bladed Main Rotor, an Allied Signal TSE-331-10 turbine engine, extensive engine soundproofing, and a maximum gross weight of 7,700 lbs. NASA testing at the time showed it was the world’s quietest helicopter. It was designed for Papillion Helicopters Grand Canyon Tours. Two S-55QT helicopters are, at the time of this writing, presently operated by Whisper Jet Inc. for hire in a utility role.
S-55QT N17756 five bladed, turbine powered S-55
.
The S-55 was featured in the Sikorsky Archives Newsletter in July, 2002. A link is provided below.
The link below provides a trip down memory lane to experience the sights and sounds of an S-55B helicopter.
.
NOTE: Links in this document to websites outside the Archives site are provided to supplement the information provided. A reference to these sites does not constitute an endorsement or a confirmation of the historical accuracy of the information by the Igor I. Sikorsky Historical Archives, Inc.
Prepared by Vinny Devine
November 2012
.for further reading see NEWSLETTER APRIL 2011 and
NEWSLETTER JULY 2012

.last update JANUARY 10, 2013
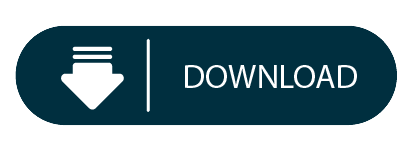